In its gigafactories and workshops, Tesla could be discreetly pioneering a revolution in the electric car manufacturing process.
Elon Musk, Tesla’s CEO, has always been a fan of “unboxed” production : making large sub-units of a car and then snapping the modules together. The EV company was “gigacasting” a few big parts—using ultra-high pressure presses to mold these pieces—instead of hundreds of small ones long before rival automakers started thinking about it . Now Tesla is pushing the envelope further by testing even bigger presses to cast virtually the entire body of a car. Side Mirror
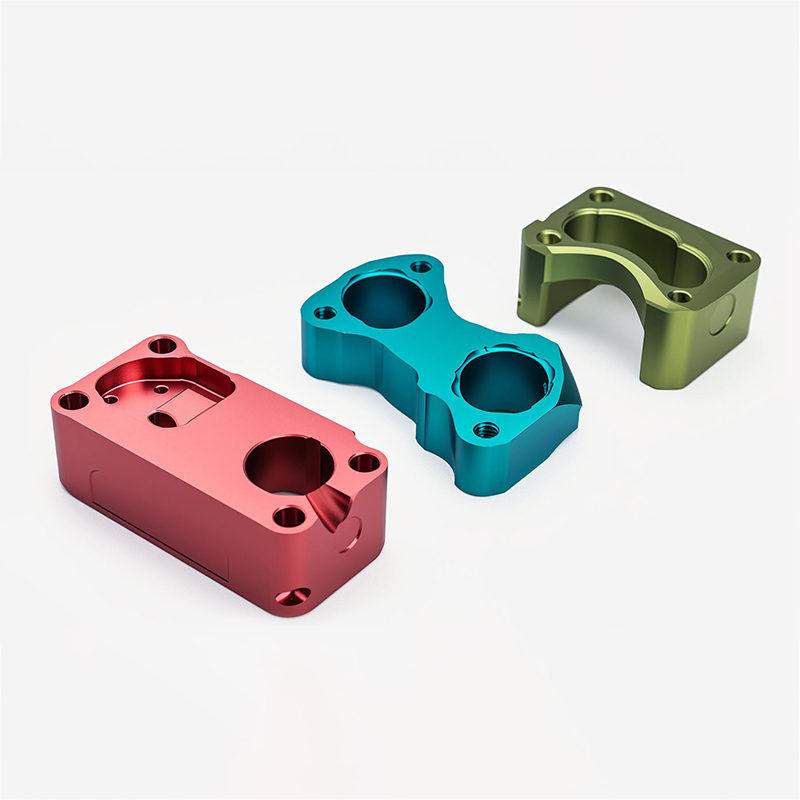
Tesla’s secret new technique combines 3D printing and industrial sand, Reuters reported , citing five sources familiar with the process that is still under wraps.
According to these sources, Tesla will use a mold comprising 3D-printed solid sand cores inside; the sand will be removed after casting, leaving a hollow subframe for structural soundness, the Verge explained . This process gives Tesla more wiggle room to make adjustments in terms of cost, design, and time than traditional metal molds.
Scaled up, this technique could Tesla closer to Musk’s goal of halving production costs . At a smaller scale, Apple’s unibody design for its laptops—where the full structure of the product comes from machining one aluminum slab—helped the company save on assembly costs.
6,000 to 9,000 tons: The clamping pressure to mold the front and rear structures of its Model Y, in a “gigacasting” process
10 hours: How quickly Tesla can churn out a Model Y using gigapresses—about three times faster than electric cars built by competitors
16,000 tons or more: The clamping pressure that Tesla would need for its new method, which would require much more space. Tesla is doubling the size of its Berlin factory and trying to set up plants in India .
400: The number of parts conventionally used in the kind of car-building techniques that “gigacasting” will replace, according to Reuters’ sources
$25,000: The price of the small, affordable EV that Tesla plans to launch by 2025
$4 million: The cost of making a large-scale mold from scratch
$1.5 million: The cost of redoing a mold with changes after the initial test
18-24 months: How quickly Tesla could develop a car from scratch with the new technique, versus 3-4 years for most competitors
While it is not immediately clear who Tesla is collaborating with for its new presses, it has so far worked with the IDRA Group for its existing processes. The giant machine maker has been around for seven decades, and been making gigapresses since 2015 . Apparently, IDRA was the only one of the six major manufacturers in the world that didn’t turn down Musk’s requests to make the massive casting machine for Tesla’s cars.
🔋 The time to solve the electric car’s battery problem is now
🏭 Tesla seems ready to open a factory in India
🇲🇽 Tesla is the latest American manufacturer to invest in Mexico
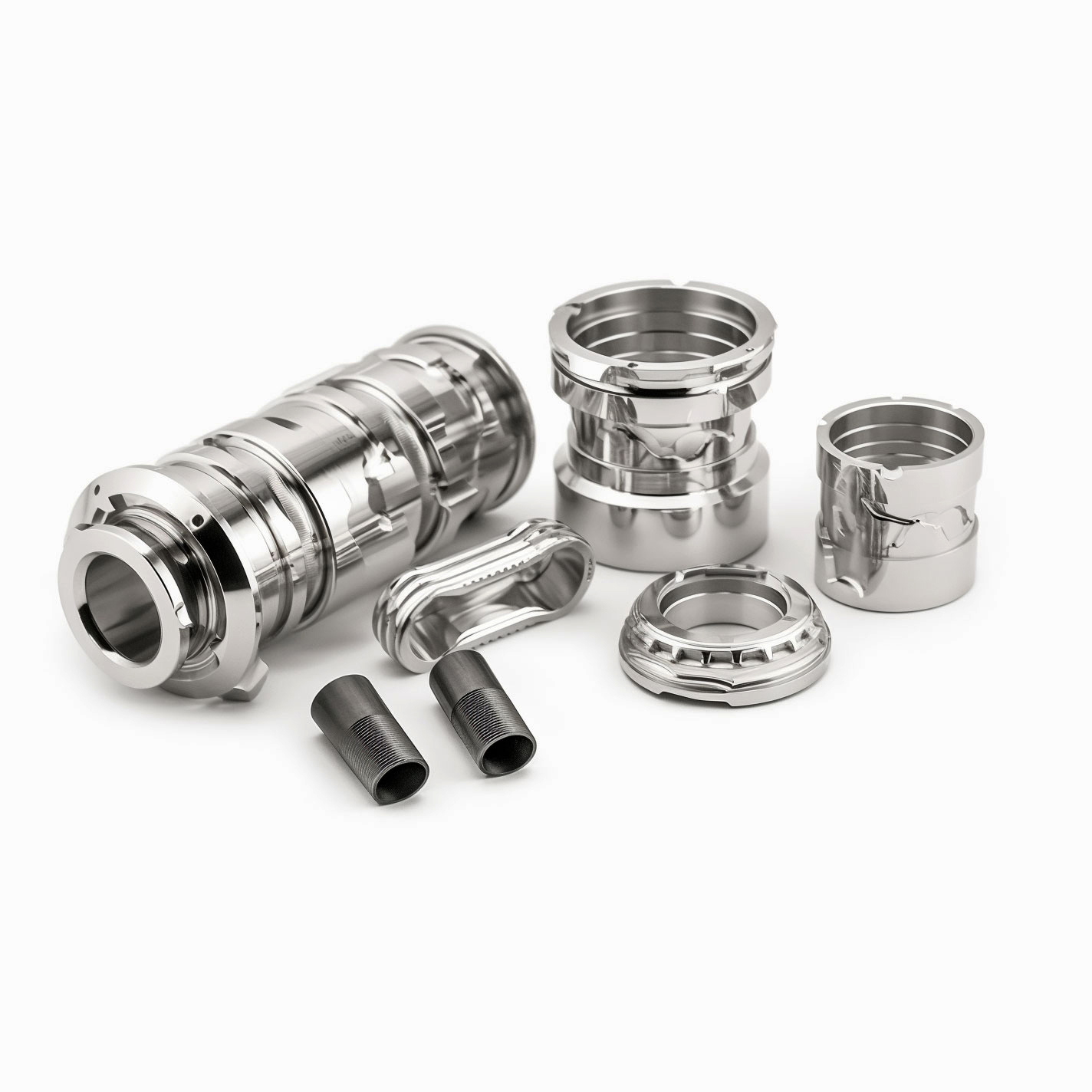
Plastic Polisher Shell Mold Our free, fast, and fun briefing on the global economy, delivered every weekday morning.