This article was updated Feb, 10, 2022. It was originally published Nov. 15, 2002.
RELATED: Investment Casting Goes Digital Cold Forging
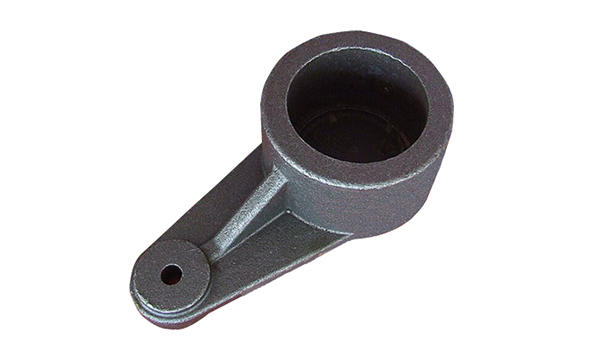
Pouring molten metal into three-dimensional molds to make metal parts is the basis behind both sand and investment casting. But there are significant differences between these two methods.
In sand casting, molten metal is poured into a sand-based two-piece mold.
Molds are created out of sand usually mixed with clay as a bonding agent and moistened with water. The sand is compacted around a full-sized pattern or model of the final product. Technicians split the mold apart and remove the pattern. The two halves of the mold are put back together, leaving a void the exact shape as the pattern. The void gets filled with molten metal and, once it cools sufficiently, the mold is opened, the sand removed and the part taken out. The metals are usually iron, steel, bronze, brass, aluminum, magnesium or other non-ferrous alloys.
RELATED: NET-SHAPE Metal Parts in One Shot
Investment casting, otherwise known as lost-wax casting, also makes parts from molten metal, but usually stainless-steel alloys, brass, aluminum and carbon steel. The first step in this type of casting is to build a pattern of the final product or part out of wax, which can be done in one of three ways:
To cast several parts at once, several wax patterns can be assembled into a “tree” with wax runners and sprues carefully connecting them. The tree gets repeatedly dipped in a ceramic slurry which then hardens when it dries. After receiving several layers of ceramic that are left to harden, the tree and its patterns are heated and the wax flows out. Wax is also melted out of the sprues and gates, leaving tubes and pipelines that molten metal will flow through to completely fill the mold.
RELATED: Single-Crystal Turbine Blades Earn ASME Milestone Status
Molten metal is poured into the now-empty mold and left to solidify. The ceramic mold (i.e., the investment) is destroyed to remove the part(s).
Investment casting is often much more expensive than sand casting due to the complexity and preparation needed compared to investment casting.
With sand casting, it is comparatively simple to handle design changes by changing the mold by modifying the pattern or core boxes, which are often made of wood). It’s more complicated with investment casting; technicians may need to modify or replace the solid metal pattern, or make new molds for turning out wax versions. But sand casting cannot always make the small, intricate parts possible with investment casting.
Another major difference between the two is the final part’s surface finish. With sand casting, works must split the mold to remove the final product. As a result, finished parts end up with a seam made by parting lines in the mold. And the sand, which is relatively rough, leaves the cast part with an equally rough surface. The parting line and roughness often are smoothed over in post-processing, which calls for more time, labor and money.
The ceramic molds used in investment casting are hard and as smooth as the original was patterned. Finished parts have smooth surfaces, tight tolerances, and they can have thin walls. After removing the gates and sprues, parts often don’t need to be processed any longer; they are finished.
Investment casting uses liquid slurry to form the molds, so cast parts can have almost any shape. This gives engineers extraordinary design flexibility to add intricate features and complex, imaginative shapes. Sand-cast parts usually must be tapered (with draft angles) or shaped so they easily come out of the packed sand. It’s also a challenge to sand-cast parts with internal voids or cavities. This requires cores accurately shaped and placed in the mold to form the interior. Several cores may be required, and it can be a time-consuming chore to form and secure each in every mold.
RELATED: Designing for Investment Casting
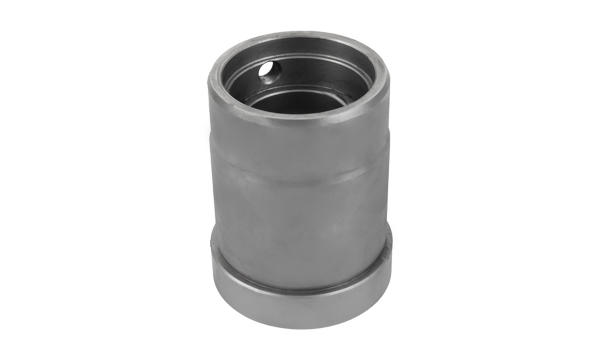
Cnc Milling Machine Parts Brad Done was a vice president at Reliance Foundry Co. Ltd., British Columbia, Canada, when this article was originally published.