The new CD110 capacitor discharge stud welder from Image Industries welds studs in as little as 0.01 second. Charge time is less than 3 seconds. Photo courtesy Image Industries Inc.
The new NCD+ 3200 capacitor discharge welder from Nelson Stud Welding is microprocessor-controlled. It can weld studs up to 3/8 inch in diameter on steel, stainless steel, aluminum, copper, and brass. Photo courtesy Nelson Stud Welding Inc. Produt U Bolt
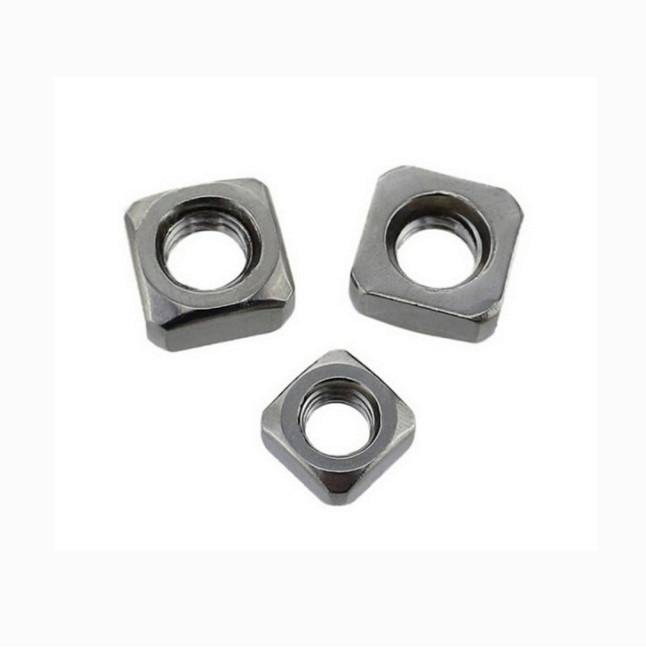
Threaded studs are the most common fastener for stud welding, but the technology can also be used to attach pins, tabs, hooks, loops, brackets and hydraulic fittings. Photo courtesy Image Industries Inc.
The new KSE 1000s from Nelson Stud Welding is a servo-driven weld head for automated, drawn-arc stud welding applications. Photo courtesy Nelson Stud Welding Inc.
A robot can weld multiple studs per minute, depending on the fastener size and materials. Nelson Stud Welding is working on new technology that could weld up 20 studs per minute. Photo courtesy Nelson Stud Welding Inc.
Stud welding has numerous applications in the automotive industry. Photo courtesy Boehm Pressed Steel
Stud welding is readily automated. In this cell, robots present parts to stationary welders. However, welding guns can also be mounted to a robot. Photo courtesy The Roueche Co. LLC
For automated applications, studs can be fed from a vibratory bowl and blown to the weld gun via a pneumatic hose. Photo courtesy Solysol.
These days, manufacturers of all stripes are taking a closer at their energy consumption as a potential source of cost savings—even manufacturers of the largest, most expensive products in the world.
The General Dynamics Bath Iron Works in Bath, Maine, builds destroyers and other warships for the U.S. Navy. Although one destroyer can cost upwards of $640 million, that didn’t stop the defense giant from examining the cost of installing one of the smallest and lowest tech parts on the boat: the studs, pins, brackets and other fasteners welded to frames, walls and bulkheads.
One Navy ship can contain millions of these welded fasteners. Thus, a few years ago, General Dynamics and fellow shipbuilder Huntington Ingalls Industries Inc. teamed up with Nelson Stud Welding Inc. to quantify how much energy they could save by swapping out their old stud welding equipment for newer, more energy-efficient models. Their results, published in May 2012, were startling.
Specifically, the study compared newer models of drawn-arc stud welders (equipped with inverter power sources) with older models (equipped with timer boxes or transformer-rectifier technology). The study also compared newer models of capacitor-discharge stud welders (equipped with switch mode power sources) with older models (equipped with transformer-rectifier technology). The equipment was tested both in a controlled lab environment and in various shipyards.
The researchers found that, due to their low duty cycle, stud welders consume the most energy when they are actually idle. In contrast, the newest equipment consumes 20 to 24 times less power at idle. The researchers estimated that $842 to $1,013 per power source per year—or $0.128 to $0.154 per stud—could be saved if their old stud welding technology were replaced. By upgrading 700 older stud welders with newer models, the shipbuilders could save, collectively, between $589,000 and $708,000 annually. (To download the report, click here: http://bit.ly/1nCqtSp.)
Stud welding is a process by which a metal stud is joined to a metal workpiece by heating both parts with an arc of electricity. The workpiece need only be accessible from one side.
A variety of fasteners can be welded with this method, including threaded studs, pins, tabs, tapped sockets, hooks, loops, brackets, hydraulic fittings, and special hardware adapted to a specific task, such as securing hoses or wire harnesses.
The technology is used in myriad industries and applications. In the automotive industry, for example, it’s used on heat shields, power steering assemblies, exhaust systems and other components. It’s also used on aerospace assemblies, tractors, commercial dishwashers, office furniture, air conditioners, barbecue grills and cookware.
There are two basic technologies for stud welding: drawn arc and capacitor discharge.
The drawn arc technique requires a DC power supply to create the arc, a weld gun, and a disposable ceramic ferrule, which concentrates the heat and contains the molten pool of metal. The stud is loaded into the gun’s chuck and a ferrule is placed over the end. The gun is then placed against the workpiece.
When the trigger is pulled, the power supply sends a signal that energizes the gun’s internal lift mechanism, lifting the stud and drawing a pilot arc. This arc establishes a path for the weld current, which follows immediately after.
After enough arcing time, a weld pool forms and the lift mechanism is de-energized. This causes the stud to plunge into the molten metal. As the stud and the base metal join, the metal cools and the weld is formed. Flux embedded in the stud vaporizes during the operation to keep the weld zone clean.
The capacitor discharge technique requires a weld gun and a capacitor storage system to produce a rapid electrical discharge. Ferrules and flux are not needed, but the stud must have a special projection on the end to be welded.
There are two techniques for capacitor discharge welding: contact and gap. In contact welding, the stud is loaded into the gun and positioned in contact with the workpiece. Energy is then instantaneously discharged from the capacitors through the stud’s projection. The projection vaporizes, creating a gap that allows an arc to be formed. As the stud and workpiece begin to melt, they are forced together, and the weld is produced. In gap welding, the stud is positioned above the workpiece rather than on it.
“Capacitor discharge is a very quick process,” explains Blake Hobson, co-owner of Image Industries Inc. “Weld times range from 2 to 12 milliseconds, and penetration depth into the base material is low—0.002 to 0.004 inch.
“With arc welding, you can have weld times from 50 milliseconds to 1.5 seconds. Penetration into the base material could be as high as 0.125 inch.
“Capacitor discharge is best for applications requiring a cosmetic appearance. Drawn arc welding is more for structural applications.”
Technologically, the biggest changes in stud welding technology have come in the power supplies.
“Traditionally, drawn arc units have been powered by transformer rectifiers with really large transformers,” says Doug Phillips, director of product management at Nelson Stud Welding. “As long as the unit is powered up, it’s consuming electricity at a very high rate just to keep the transformer going. And, of course, it’s consuming additional electricity when it’s welding.
“Now, drawn arc units are available with inverter power supplies. These welders have dramatically smaller transformers. They switch primary power on the transformer at a very high speed, so losses from the transformer are only seen when the unit is actually welding. When the unit is not welding, it uses very little power.”
Inverter technology is more costly, however. “Most manufacturers still use transformer rectifiers for drawn arc stud welding,” concedes Hobson. “Inverters are still very expensive.”
Aside from better power supplies, improvements in stud welding technology have been mostly incremental. Lighter weight, servo-driven weld heads are facilitating automated welding applications. Microprocessor control is enabling engineers to set and monitor process variables such as current, voltage and time. Changes in the amount of energy consumed during a weld could indicate a bad assembly.
Some suppliers now offer equipment that can run more than one weld gun. That enables one power supply to serve more than one welding station, or it allows one station to be equipped with multiple guns. For example, one gun could be reserved for 1/4-inch fasteners while another could be set up for 5/8-inch fasteners. That saves setup time.
“Changing over a chuck is only a 5-minute chore, but if you do that 10 to 15 times a day, you can lose more than an hour of production,” Hobson points out. A
To reduce vehicle weight, automakers are increasingly using high-alloyed steel in body components. Because the material is so strong, automakers can get away with using very thin sheets.
But, what’s good for cutting weight is not so optimal for stud welding. Even capacitor discharge stud welding reaches its limits at a wall thickness of 0.5 millimeter. Even when welding is viable, it’s often not desirable for cosmetic reasons.
To solve this problem, DELO Industrial Adhesives LLC and fastener manufacturer Böllhoff Inc. have developed an alternative to welding for attaching studs to thin sheets—bonding with a UV-curing adhesive.
Called ONSERT, the new technology pairs a UV-curing adhesive (an acrylate or epoxy) with a special bi-material fastener. The fastener consists of a metal stud or insert with a flange molded from translucent or transparent plastic. The plastic allows UV light to reach the joint line and cure the adhesive in less than 5 seconds.
The technique can be used on both metallic and nonmetallic substrates, including glass, plastic and carbon-fiber-reinforced polymer. It can even be used on metals that have received a surface treatment, such as cathodic dip coating.
One side benefit of stud bonding is that it requires significantly less energy than welding. To weld a stud 6 millimeters in diameter to a zinc-plated steel sheet 1 millimeter thick, a welder might need to apply 18 kiloamperes of current for 100 milliseconds. That consumes 3.6 kilojoules of energy.
In contrast, an LED might need to shine UV light at a wavelength of 400 nanometers on the joint for 5 seconds. That consumes only 0.6 kilojoule.
For more information, visit www.boellhoff.com/en/de/assembly_systems/adhesion_of_fasteners.php.
You must have JavaScript enabled to enjoy a limited number of articles over the next 30 days.
Connecting shop floor tools to a manufacturing execution system is critical to error-proofing assembly processes, improving quality control, and lowering defect and scrap rates. Join Torrence Williams, Partnerships Manager for Pico MES, and Dan Smith, VP of Sales for Kolver Tools, as they discuss an easier path for manufacturers to start connecting their factory floor.
This topic is something that challenges each of us every day that we go to work. This talk is about change and why it works and why it fails. It is focused on manufacturing facilities, because that is where the author has spent most of his working life.
Copyright ©2023. All Rights Reserved BNP Media.
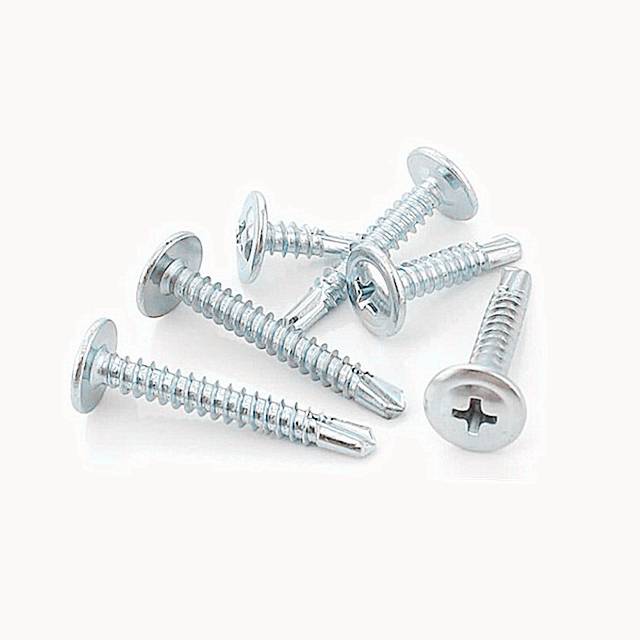
8.8 Grade Bolt Design, CMS, Hosting & Web Development :: ePublishing